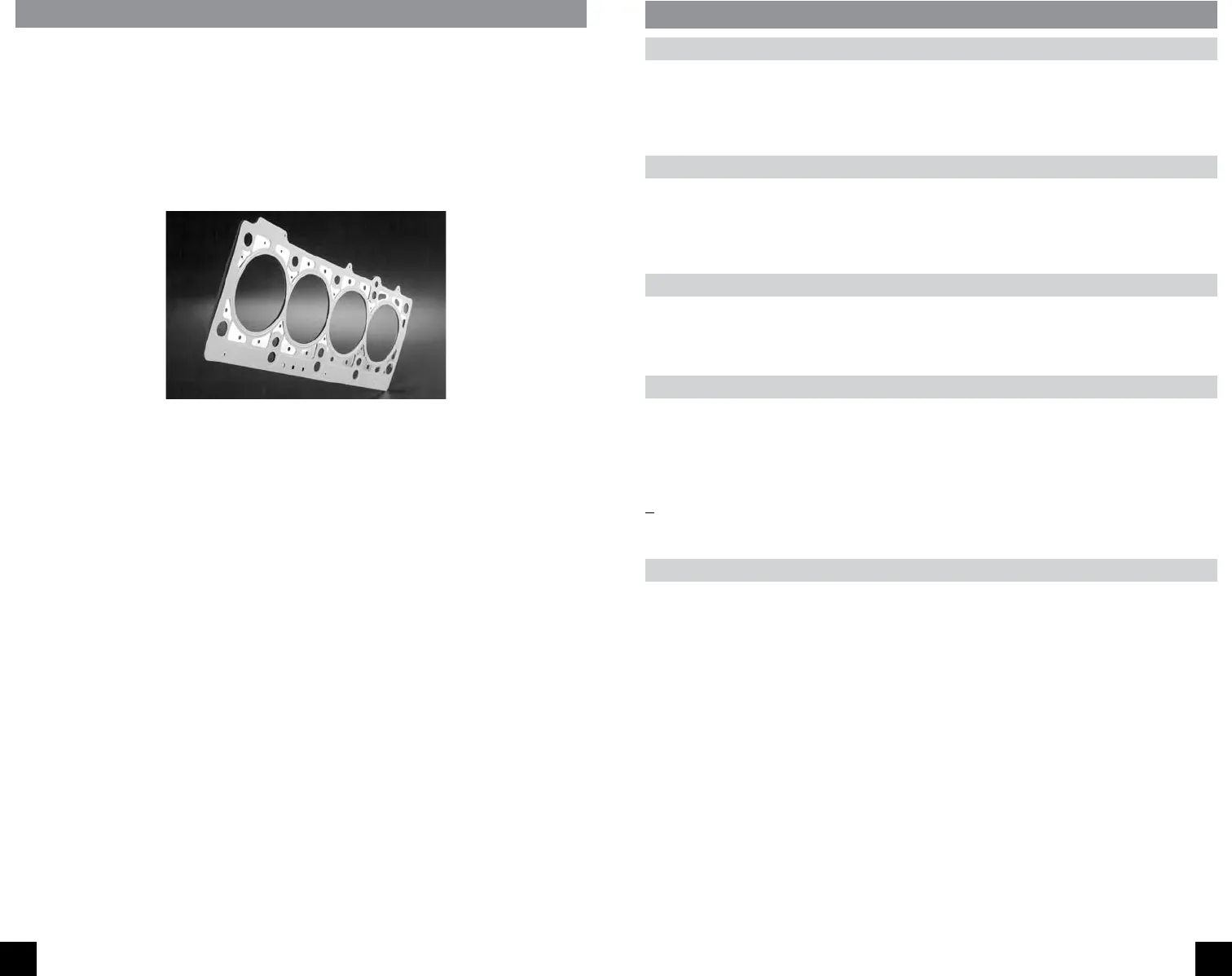
The latest development in head gasket technology is the multi-layer
steel (MLS) design.
At first glance, these gaskets look like the old-style embossed steel shim gaskets, but
they are radically different. First, a thin rubber coating is bonded to the stainless steel
shim and, as required, multiple layers (up to five) of this rubber-coated steel shim
are assembled into a single gasket. The high-temperature rubber coating provides
excellent fluid sealability across the outer faces and between the individual layers,
while also sealing minor head and block surface imperfections. MLS head gaskets
provide the ultimate in torque retention and supply extra strength to support current
lightweight aluminum casting designs. They are specified on most current domestic
and imported engines in production.
Traditional original equipment manufacturer (OEM) type MLS head gaskets don’t
easily conform to surface irregularities, and require an incredibly smooth surface finish
to provide a satisfactory seal. When the castings are new and the finish is fresh, most
OEM-style MLS gaskets work quite well. But when the castings are old or resurfaced
with a less than perfect finish, leaks usually result.
To seal under these adverse conditions, FEL-PRO
®
engineers have developed the exclusive
PermaTorqueMLS
®
design. These newly redesigned MLS gaskets have many unique
features that
allow them to seal better than other MLS gaskets on the market today
:
•Full-hardstainlesssteelmaintainsitsshapedespitethermalexpansion,and
resists the scrubbing action between head and block
•Precision-engineeredembossedsealingbeadsplacedatallcriticalsealing
areas to eliminate leak paths
•Anexclusiveextra-strong“stopper”layerincorporatedtoprovideasuperior
primary combustion seal
•Specialrubbercoatingspecificallyformulatedfortheaftermarketrepair
environment, which is more forgiving of surface finish requirements
Remeber that although PermaTorque MLS head gaskets are more forgiving than other
designs, the finish on both the head and block must be flatter and smoother than what
has been traditionally required for composite-type gaskets.
FEL-PRO
®
engineers determine which PermaTorque construction provides the best
sealing for each individual engine design. Look for the “PT” suffix on the FEL-PRO
part number for PermaTorque head gaskets, the most reliable no-retorque designs
available on the market today.
FEL-PRO
®
PermaTorque
®
CYLINDER HEAD GASKETS
Remove Cylinder Heads Carefully
Loosen the head bolts in stages, in the reverse order of the tightening sequence. On
engines with aluminum cylinder heads, remove the head only after the engine has cooled
completely and reverse EXACTLY the recommended torquing procedure. Failure to do
so may result in head warpage.
Never Reuse Head Gaskets
When a new head gasket is installed, it conforms to the microscopic surface irregularities
of the cylinder head and engine block. The gasket material is permanently compressed in
that position. If you reuse the gasket, it is impossible to refit it in the exact same position
and it will not have the “life” to readjust itself, so gasket failure may result.
Clean Mating Surfaces
Thoroughly clean the cylinder head, engine block, head bolts, and bolt holes. A dirty bolt
can alter torque readings by as much as 20 foot-pounds, and can form pockets in the
gasket allowing leakage and eventual gasket failure.
Check for Warpage and Distortion
Check for warpage of both head and block sealing surfaces with a straightedge and a feeler
gauge. Out-of-flat along the length should not be more than 0.003" for three-cylinder
applications, 0.004" for four-cylinder applications, and 0.006" for six-cylinder applications.
Across the width should never exceed 0.002" out-of-flat. These are combined measurements
for both the head and block together, and should not exceed the maximum amounts shown.
There should be no sudden irregularities exceeding .001" and a maximum out-of-flat of
+ .001" in any 3" diameter should not be exceeded. When necessary, machine surfaces
to return them to flat.
Check Head and Block Finishes
Surface finish is critical for a good seal. FEL-PRO
®
engineers recommend a micro inch
surface finish between 60 to 100 Ra (400 to 800 Rz) for cast iron heads and blocks,
50 to 60 Ra (200 to 600 Rz) for aluminum heads and blocks, and 10 to 30 Ra maximum
(500 Rz maximum) for multi-layered steel (MLS)
applications. Check the finishes with a
profilometer or another type of surface finish comparator
. Check for a preferred waviness
height of .0004"/.0005" with a waviness peak spacing of .100" (these values are usually
associated with milling machines). Always consult your manufacturer’s service manual
for surface finish requirements.
CYLINDER HEAD GASKET INSTALLATION TIPS