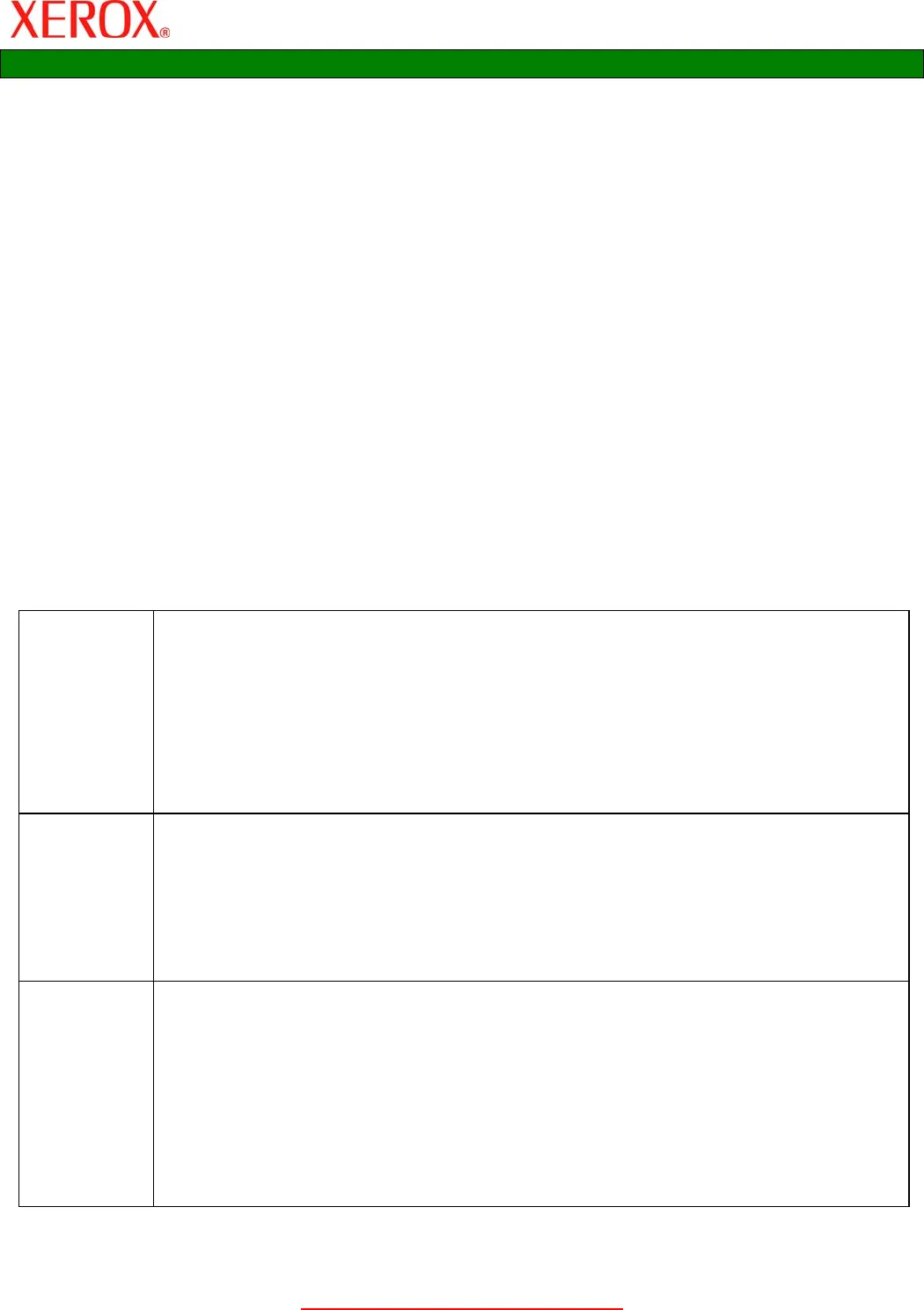
Lamination Overview
Introduction
Lamination can be the most critical portion of graphics construction. Finishing the print offers a value-added
service by the print provider that can produce higher revenues per print. Lamination protects the print from
mechanical damage that may be caused by contact, handling or abrasion, but an over-laminate also protects
prints from colour deterioration preventing reaction of atmospheric components with colourants over time.
• Laminate a graphic if it is to be exposed to extreme conditions or abrasion.
• Lamination adds a gloss or lustre finish, as well as enhancing colours (without altering the colour)
depending on the laminate used.
• If the print is displayed under harsh lighting, use a matt finish to reduce glare.
• Use heavier grades of laminate to add bulk and stiffen prints or add a high gloss appearance.
Inappropriate lamination technique is the leading cause of material waste. This information is intended to be a
starting point. Each laminator has its own characteristics, which vary depending upon ambient conditions,
laminator model, settings and adjustments, age and condition of the laminator, etc. Temperature, pressure,
speed and tension adjustments may need to be made to optimise laminate bond and to obtain flat graphics.
Generally, do NOT use low-melt laminates with oil inkjet prints. Xerox oil inkjet media
require hot-melt thermal adhesive. Delamination can occur if the heat and pressure
settings used are inappropriate specifically for oil inkjet prints: Oil inkjet requirements for
laminating differ from aqueous and solvent inkjet prints.
Understanding Laminates
Use the appropriate laminate for your media and your application. Check the appropriate media specification
sheet to verify if certain laminates are not appropriate.
Laminate
Types
THERMAL laminates consist of a polyester (PET) face film with heat-activated adhesive on
one side. With heat applied to the adhesive via the laminator the adhesive melts
(activates). Once the heat source is removed it sets within a few seconds.
PRESSURE SENSITIVE laminates have a pressure sensitive adhesive applied to one side.
This type of lamination does not use heat to activate the adhesive. Adhesive is activated by
pressure alone.
PET based laminates are durable and tough, with high tear and impact strength, excellent
scratch resistance, and flexibility once applied. Since PET laminates do not contain
plasticisers, they do not become brittle with age under normal conditions
Laminate
"Looks"
GLOSS: provides maximum clarity and colour enhancement and is used when the customer
desires a ‘photo-glossy’ look.
SATIN / LUSTRE: gives a less glossy finish while maintaining excellent clarity and colour
enhancement - should be used when there is concern about light reflections (glare) but the
image benefits from some degree of gloss.
MATT: least glossy finish while maintaining good clarity and colour enhancement and
should be used to eliminate or minimise glare.
Laminate
Composition
A lamination film is a post-printing material made of two parts: polyester and adhesive.
"Construction" refers to the film and glue relationship. Construction is typically described by
micron or mil thickness, eg. 5mil laminate will be described as a having a 3/2 construction
(3 mil polyester / 2 mil adhesive). 1 mil = 25 microns
It is the polyester that affects colour saturation and gives you rigidity. The greater the ratio
of polyester to adhesive, the better the quality of film. A 5 mil laminate with a 3/2
construction is higher quality than a 5 mil laminate with a 1/4 construction.
All laminates are not the same. Typically laminates that have thinner face films (economy
construction) will be more problematic then those with a thicker polyester layer. Thinner
face films will stretch and distort more easily creating wrinkles and other image defects.
www.xerox.com/iccprofiles.com
35