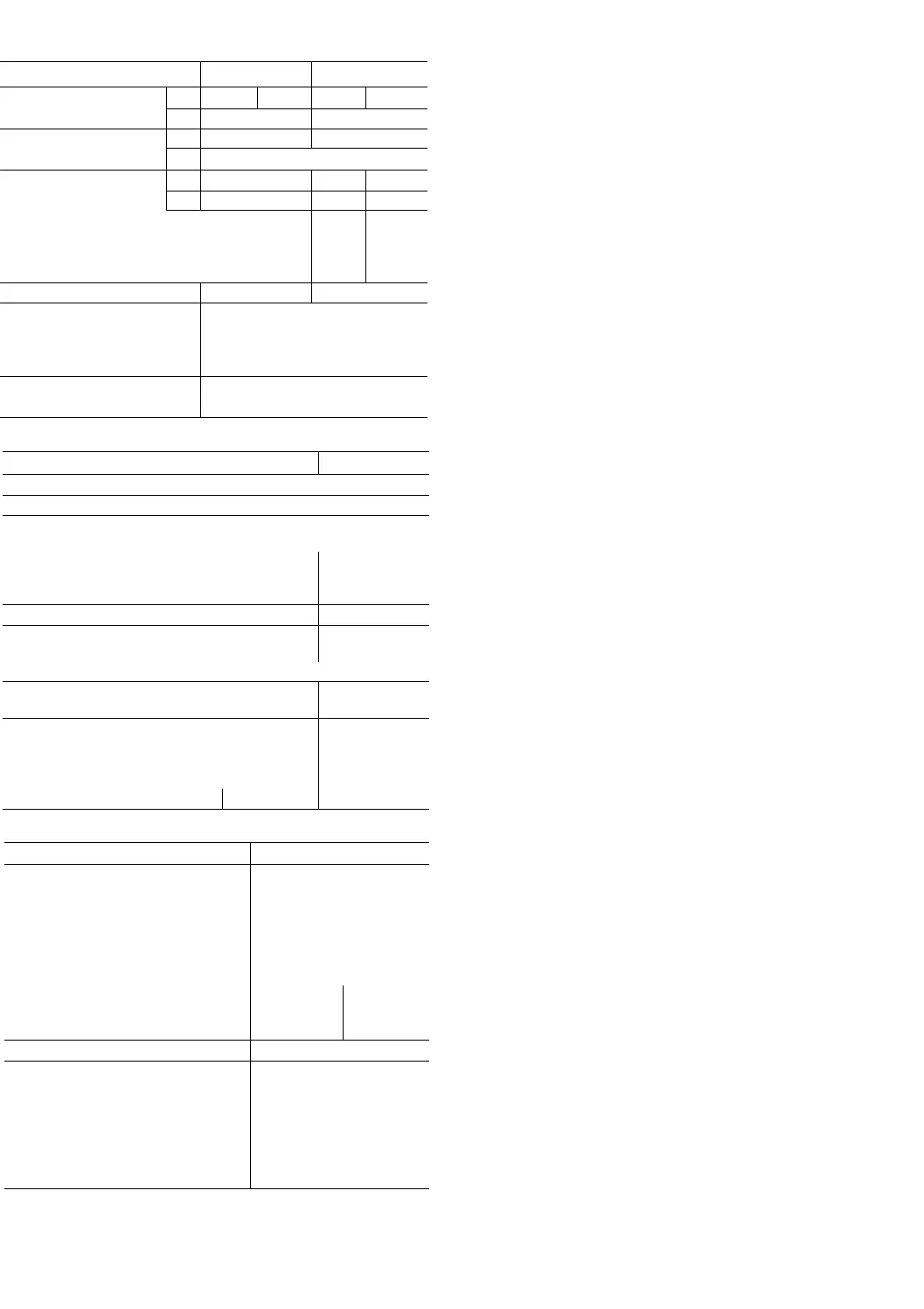
UNIT AND COMPRESSOR
Table 2 — Physical Data
UNIT 30HK.HL
015
020 025 030
APPROXIMATE
HK
1637
1787
1980 1985
OPERATING WT (lb)
HL
1016
1136 1310
1334
REFRIGERANT(R-22)
HK
34
38 40
45
CHARGE (lb)
HL
Holding Charge
COMPRESSOR 06*
HK DC537
E2150 E7265 E7175
HL DC537 E2250 E7265 E7275
No. Cylinders
6
4
6
6
Oil Charge (pt)t
8.5 14
19 19
No. of Unioaders
2 1 2 2
Cap. Control Steps
3
3 3
3
CONDENSER. 09RP (HK) 022
027
MAX DESIGN WORKING
PRESSURE (psig)
_ , ( Water Side
Cooler i „ , - .
< Refrig Side
150
235
„ . f Water Side
Condenser Side
250
385
COOLER
COOLER10HA400
774 784
UNIT 30HK.HL 015,020
025,030
SHELL, Net Vol. (Gal.)t 6.8 9.9
TUBES (Copper) Internal Fins,
5/8-in. OD X 0.020 wall
Number 81
81
Length (in.)
62.5 85.5
Eff. Outside Surface (sq ft)
66.3 91.7
REFRIGERANT CIRCUITS
1 1
CONNECTIONS (in.)
Water 1
^ ( Drain (MPT)
2 2
3/4
3/4
Refrig
< Suction
I 1.125 1.125
1.625 ODM
2.125 ODM
WEIGHTS (lb)
Cooler (Net)
354
446
Water
75
100
Refrigerant 8 12
Total
437 558
CONDENSER
09RP 022
027
TUBES Copper, Integral Fins
OD (in.) 3/4
Wall Thickness (in.)
Plain End
0.043
Finned Section
0.028
Length (in.)
10^7
Fins/in.
40
Number"
36 44
32.9
40 2
Surface Area (sq ft) i .
! Outside
133.6
163.4
NO. WATER PASSES
CONNECTIONS (in.)
... , ( In (IPS)
^ f Out (IPS)
2/2 Sched 40
2/2 Sched 40
Relief Valve Outlet (SAE)
Ув
Water Regulating Valve /4
Liquid Outlet (ODF) /в
Hot Gas (ODF)
13/в
'Prefix; 2 = 1 electric unloader; C, 7 = 2 electric unloaders.
tSee Check Oil Charge for Carrier-approved oil.
+ lncludes nozzles.
"Includes 5 subcooler tubes.
Only electrical power connections and water con
nections for condenser and cooler are required for
HK installation. Installation of HL units varies only
in field piping required for the remote condenser.
Step 3 — Check Compressor Mounting and
Connections
As shipped, compressor is held down by special
self-locking bolts and plain lock washers. After unit
is installed, remove self-locking bolts one at a time
and reassemble with flanged washers and neoprene
snubbers as shown in Fig. 2. Special flanged washers
and neoprene snubbers are shipped in a cloth bag
tied to one of the compressor feet. Tighten all 4
bolts. Then loosen each until flanged washer can be
moved sideways with finger pressure.
t’.-M "! ION: iie sure mierconnecting piping and
electrical condu■'.^ aic suspended Irec oi contact
with any adjacent wails, and be sure unit capil-
k;:;cs are nol rur'-.nmg aguinst ;i::>thing.
SERVICE ACCESS
Remove combination top and back cover over
compressor. Servicing can be performed from either
top or back. For rear access, allow approximately
3 ft of clear space behind unit.
Step 4 — Make Piping Connections
CONDENSER DESCRIPTION
The condenser is a sheli-and-tube type with
removable heads for easy tube servicing. Condenser
has an internal subcooler designed for 12- 15 F total
liquid subcooling at average tower water conditions.
For further condenser data refer to Table 2, Physi
cal Data.
CONDENSER PIPING
Provide a means for draining system in winter
and for maintenance.
1MP(.)R 1 ,-\N i ; L -.mdeu.sc: v>a*.cr ntust enter at
ho:tom I;.;- proper operation ot the intcrual .sub-
cooler in condenser bottom (Fig. I).
Keep water supply lines as short as possible. Si/e
lines according to available head pressure, rather
than by connection size, especially on cooling
tower applications. Use flexible connections to
reduce vibration transmission. Refer to Carrier
System Design Manual, Part 3, Piping Design.
The 30HL units using air-cooled or evaporative
condenser should have adequate means for head
pressure control when operating below 60 F outdoor
ambient temperature.
A water regulating valve must be installed on
cooling tower application when any of the following
conditions exists:
1. Low outdoor ambient temperatures affect head
pressure.
2. Entering chilled water temperature is below 70 F.
1090